The ability to store harvested canola without seed quality deterioration is critical to Western Canadian farmers, as it enables them to plan marketing and delivery options more effectively. Harvested canola seed has a high concentration of oil, so it can be more volatile in storage than other grains grown on the Prairies. As a result, extra care must be taken to properly condition stored canola in order to maintain quality.
- The main factors impacting the safety of stored canola are moisture content, temperature, dockage, moulds, and green seed content.
- Condition canola to eight per cent moisture content and less than 15 degrees Celsius as soon as possible after harvest, for safe long-term storage.
- Monitor storage facilities closely within the first six weeks after harvest when seed respiration can be high. Regular monitoring should occur throughout the winter.
Importance of storage and conditioning canola
Stored canola is susceptible to heating, which justifies extra care after placing it into storage. Bulk canola contains seeds of varying ripeness and surface-borne fungi from the field, which may lead to respiration (or “sweating”) before becoming fully dormant. Fully ripened seeds with low moisture content are metabolically dormant and respiration is negligible1.
Respiration can also be caused by convection currents within the bin that can quickly develop when grain with varying temperature and moisture levels are combined in the same bin (different loads that have been deposited at different levels within the bin). Dockage is known to accumulate at bin walls during unloading and can be significantly higher in moisture content than the harvested canola seed2. However, researchers have monitored freshly-harvested canola in steel bins and found no evidence of an initial “sweating” process3,4.
Regular monitoring is required because increases in temperature and moisture favour the growth of storage moulds. Mould growth and respiration produces additional heat and moisture, which can cause the temperature within the seed bulk to quickly increase, which may lead to head-damaged seeds.
The term conditioning refers to processes involving the movement of air through stored seed to ensure safe storage over a period of time. Conditioning systems are used to cool or dry harvested hot or moist seed to avoid spoilage in storage. These systems also help to prevent moisture migration caused by temperature gradients within a bin, which can occur in moist seed. Conditioning also reduces respiration and is even used in regions where the seed can be harvested at optimal moisture contents and environmental conditions. Conditioning systems can extend the harvest season, since canola can be removed from the field in a tough (greater than 10.1 per cent moisture) or damp (greater than 12.5 per cent moisture) conditions, therefore allowing harvest to begin earlier and continue later into the fall. The degree to which harvest can be extended will depend on the conditioning options available. Use of conditioning can indirectly reduce field losses, as advancing the harvest means the canola will have less exposure to weather impacts that could affect the yield and grade. The ability to condition canola also helps producers avoid harvesting and selling grain that is too dry, minimizing economic losses1
Proper operation of conditioning systems, particularly natural-air conditioning systems, is dependent on current conditions of the stored seed. Therefore, monitoring and measuring moisture content and temperature of the stored seed is necessary to avoid the risk of spoilage and to know when the conditions is satisfactory for long-term storage. Sampling once more for temperature and moisture content before long-term storage is also advisable. The most critical factor in monitoring stored seed condition is an awareness of any changes that may have occurred. Consequently, accurate monitoring requires specific locations within a bin to be sampled repeatedly. Permanent sensors in a bin add to the cost of a monitoring system. However, these ensure that measurements are always recorded at the same place, which makes it easier to recognize any variations in the condition of stored seed, which could signal a problem. Portable probes can be used effectively as well, but do not provide the same precision for repeated monitoring1.
Monitoring stored canola
Monitor bins closely during the first six weeks after harvest and continue to check stored canola regularly until the bin has been emptied. Ensure stored canola cools to 15 degrees Celsius or lower throughout the bin. When stored canola temperatures plateau, or begin to rise while outside air temperature cools through the fall and winter, be on guard for an increase in spoiled grain, as this is common in this scenario. It only takes one small hot spot to start a chain reaction that can spoil a whole bin.
Using properly-anchored bin temperature and/or moisture-monitoring cables will add to the cost of storage, but make monitoring stored grain much easier. One cable has a coverage diameter of 20 to 24 feet. Bins with a diameter greater than 24 feet will need at least three cables to adequately monitor grain temperature. More cables provide extra assurance because grain never conditions or dries consistently throughout the bulk of the stored grain. Temperature fluctuations within the bin are normal, and are based on erratic air flow patterns.
Probing through doors or roof hatches may uncover hot spotsAreas within bulk (seed) that have a higher temperature than the surrounding material (ex. in stored canola). More near the bottom and top of the bin, but does not show the current condition through the central core and at all sides of the bin.
When climbing or entering bins to probe grain, always be careful and consider the safety of yourself and of others. Reduce the risk to falling or grain entrapment by using appropriate personal protective equipment (PPE) and safety equipment such as fall harnesses, by installing ladder guards/railings, and by using ear, eye, and head PPE. When working alone it is recommended to not climb or enter a bin. However, if this is unavoidable, ensure that someone else knows that you will be doing this, so they can check in later, or ask someone close by to come over and supervise.
Factors impacting canola storage
Seed moisture
The moisture content and temperature of stored grain influences physiological processes of the seed that can lead to spoilage and heating. Canola and other seeds of high oil content are more prone to deterioration in storage than cereal grains, and must be stored at a lower moisture content to prevent the seed from moulding. Under the Canada Grains Act, the maximum moisture at which canola can be sold as straight grade (dry) is 10 per cent moisture5.
Since seed with 10 per cent moisture can be sold without penalty, this threshold is often assumed to represent a safe moisture content for long-term storage6.
However, for stored canola, the upper threshold of safe relative humidity is 70 per cent at moderate temperatures, as moulds begin to grow at this level. This is equal to 8.3 per cent moisture for canola and 13.9 per cent moisture for wheat (Triticum aestivum L.) at 25 degrees Celsius7,((Hall, C.W. 1980. Drying and storage of agricultural crops. Avi Publishing Co. Westport, Conn.)). At high grain temperatures (30 to 40 degrees Celsius), mould can occur even when moisture contents are below eight per cent8. Both moisture content and relative humidity are dependent on temperature9.
Seed temperature
The temperature and moisture of stored seed influence enzymatic, physiologic, and biological activities and ultimately drive the rate of spoilage. Temperature differences within bulk commodities favour mould development through moisture migration within the bin. The high temperature of seeds that are harvested and stored on a hot day can be retained within bulks that are not aerated for many months, due to an insulating effect of the bulk seed9.
On sunny days, canola seeds in the swath, combine hopper, truck and bin can be warmer than ambient air temperature2.
Differences in temperature result in moisture moving from warmer to colder areas of the bin. During the fall, cold air cools grain at the outside of the stored grain, and warm air with greater humidity in the centre of the bin will rise. Condensation can occur when the warm air with high humidity reaches cold seeds near the surface. This moisture and the warm temperature near the surface can lead to rapid spoilage. In late spring and summer, it is possible for moisture migration to occur in the opposite direction if ambient air (outside) temperature is warmer than the stored grain. Warming from the sun on the bin causes air to move up near the outside wall of the bin and down through the centre of the bulk. Moisture is then reabsorbed by the cooler canola seed in the centre of the bin.
Removing a portion of the seeds from the centre of the bin is a method of interrupting an increase in temperature and moisture in the central core. Significant migration occurs in canola at moisture levels as low as eight per cent, when placed into storage at high temperature and not cooled by aeration10. For a quick test of restricted ventilation, open the lid at the top of the bin and feel if the expelled air is warm on your face. If it is, ventilation and conditioning are recommended.
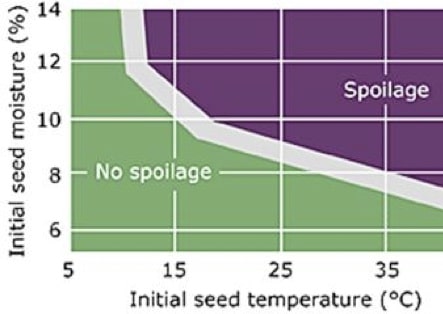
Temperature/moisture interaction
The moisture content and temperature of stored canola determines the amount of time it is safe to be stored for. The storage time chart shown predicts the ability of canola to maintain quality over five months, under varying temperatures and moisture.
If the temperature or moisture content of stored canola falls within the spoilage range, either the seed moisture content, seed temperature, or both, must be reduced. Moisture content levels can be reduced by either delaying harvest to allow for further drying in the field, or by drying the seed after it has been harvested.
Aerating stored grain can reduce the temperature of the seed. If the harvested seed is put in the bin at above 25 degrees Celsius, or if pockets of immature seeds or green weed seeds are present, 8.3 per cent moisture is too high for safe long-term storage. For longer than five months of storage, canola should be at a maximum of eight per cent moisture and at a cool temperature9.
To disrupt the moisture cycle and cool the stored canola when outside air temperatures have cooled, move one-third of the canola out of a full bin.
To successfully store canola for periods of six to 24 months, attention must be given to conditioning and monitoring. High quality seed can be stored for two to three years if moisture content and temperature are properly maintained1.
Green seed
An early frost can cause damage and decrease the seed quality of canola if it has not yet reached physiological maturity. In late August 1982, a frost halted both reproductive and seed development in canola crops over a large canola growing area of Manitoba and Saskatchewan, resulting in approximately 38 per cent of the crop being graded No. 3 Canada or Sample, compared to four per cent of the crop in these grades in 1981. Quality changes were observed in 60 bins of farm-stored canola monitored within a 200-kilometre radius of Winnipeg, Manitoba from November 1982 to April 1983. In November, the seed temperature of one bin reached 102 degrees Celsius with steam rising from the centre of the bin. Meanwhile, corresponding temperatures for non-heating bins were only at eight to 13 degrees Celsius. Generally the quality of seeds in official grades No. 2 Canada, No. 3 Canada and Sample did not decline in storage. The percentage of green seeds declined slightly in 28 bins of B. napusAlso referred to as Argentine canola, it is the species of canola currently commonly grown in Canada. More examined during the storage period. Spoilage and heating problems in frost-damaged canola are most likely to occur during the first months of storage and can be prevented by aeration, careful bin management with frequent monitoring, and the use of small, readily accessible granaries12.
Table 1: Changes in frost-damage induced green seed in stored canola between November and April
Moulds
Seeds in storage provide a good substrate for storage moulds, the most prominent cause of seed deterioration13.
Mould spores, found in the soil and on decaying plant material in the field, can coat seeds during harvest. Fungi common on freshly-harvested canola, such as Alternaria and Cladosporium, tend to decline during early storage, however, if optimal conditions for fungi growth and development exist, spoilage due to this will increase4. Each species of storage mould have different levels of relative humidity and temperature which are optimal for successful and rapid growth and development. Some species, such as Eurotium amstelodami, which prefer environments with low humidity, affect seed germination, and produce water as a consequence of metabolism during their growth. Higher moisture contents enable more damaging moulds to grow. These moulds include Aspergillus candidus and some Penicillium species, all of which impair seed germination and are often associated with hot spotsAreas within bulk (seed) that have a higher temperature than the surrounding material (ex. in stored canola). More9.
Moulding and heating can occur very quickly in moist canola, and is likely to cause the stored canola to clump to each other. This can also be accompanied by an increase in the level of free fatty acids in the stored canola seeds, possibly caused by the growth of moulds14. When rolled out, heated seeds are brown instead of a normal yellow colour, and they produce a distinct tobacco-like odour in the oil and meal, which is difficult to remove by processing1. This results in reduced quality of the stored product for processing.
The rate at which moulding occurs in recently-harvested canola is of importance because of its influence on drying and storage management decisions. One study examined spoilage times of newly-harvested canola stored aerobically in tubes at five temperatures (ranging from five to 25 degrees Celsius) and seven moisture contents (ranging from six to 17 per cent). Spoilage was more rapid at the greater temperature treatments and higher moisture contents. Seed clumping preceded the appearance of visible mould colonies, while seed germination was affected much later. This suggests that seed clumping is the best criterion for determining the maximum amount of time available for drying before fungal growth, because the appearance of the seed will have already deteriorated by the time fungal colonies become visible15. Under normal harvest conditions, canola seed over 10 per cent moisture should be dried within one to two weeks to avoid spoilage.
Table 2. The maximum time (days) before visible clumping was observed in canola with varying temperature and moisture levels
Dockage
The amount of dockage in canola delivered to elevators from farms in Western Canada prior to herbicide tolerant (HT) cultivarsCultivars are variants in a species developed through the intervention of humans (despite the term 'variety' often being incorrectly used to describe this). Cultivars can be open-pollinated type, hybrid, synthetic, composite, etc. More averaged nine per cent16. However current dockage levels in HT canola are much lower17. Dockage in canola consists mainly of wild oats, other weed seeds, volunteer cereal grain, broken/damaged seeds, broken pods and soil particles. This dockage normally has a moisture content of three to four per cent higher than canola harvested canola seed. Large amounts of broken/damaged seeds influence seed respiration rate because they provide a substrate for the growth of moulds18. When putting canola in the bin, chaff will move towards the walls of the bin. Fines, or particles smaller than canola, increase the resistance to air flow, while chaff or particles larger than canola decrease the resistance. An equal proportion of fines and chaff in a canola load increases the resistance to air flow. Spreaders have not been found to distribute dockage and chaff more uniformly than spout fills19.
Oil content
The oil fraction of canola seed absorbs less moisture than the starch and protein fractions. Therefore, the equilibrium moisture content for canola is much lower than it is for wheat18 and the amount of water that must be evaporated from canola to safeguard it from moulding is greater than with cereal grain. One study found that oil degradation after two months of storage is still within tolerance limits, but longer storage may result in significant oil degradation, depending on the storage conditions20.
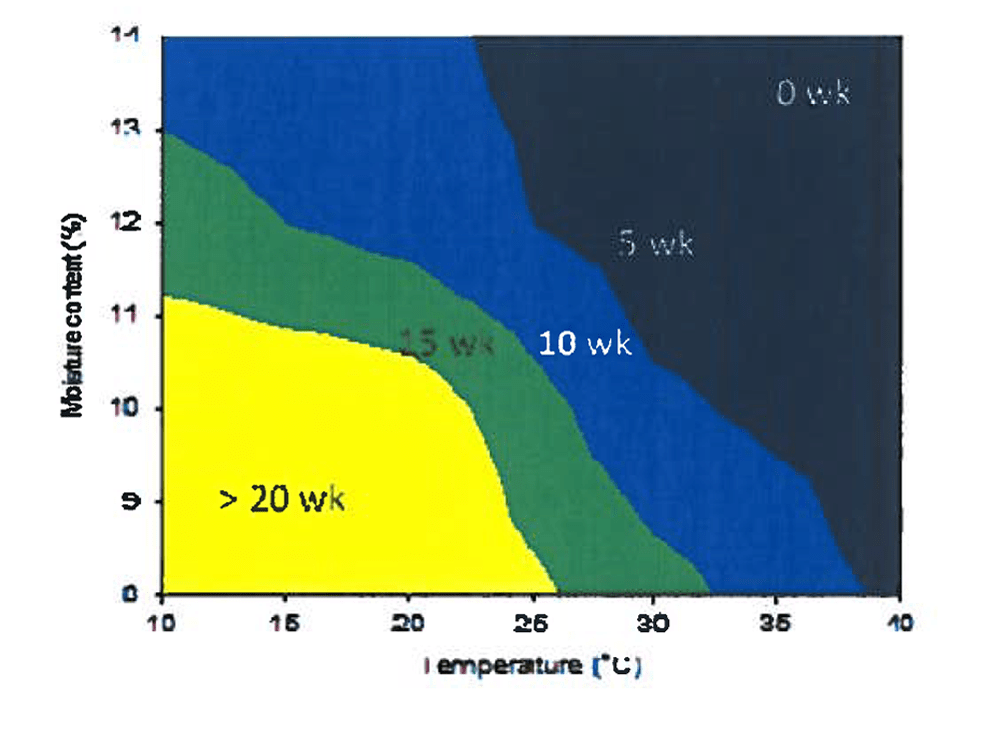
The requirements for safe storage of canola cultivarsCultivars are variants in a species developed through the intervention of humans (despite the term 'variety' often being incorrectly used to describe this). Cultivars can be open-pollinated type, hybrid, synthetic, composite, etc. More with high oil content appear to be relatively similar to those cultivarsCultivars are variants in a species developed through the intervention of humans (despite the term 'variety' often being incorrectly used to describe this). Cultivars can be open-pollinated type, hybrid, synthetic, composite, etc. More with lower oil content. Based on a 20 per cent drop in germination or the appearance of visible mould, canola with high oil content at eight per cent moisture can be safely stored at 10 degrees Celsius and 20 degrees Celsius for 20 weeks.
At 10 per cent moisture content and 10, 20, 30 and 40 degrees Celsius, canola could be stored for 20, 18, six and 2 weeks, respectively. At 12 per cent moisture content and 10 and 20 degrees Celsius canola could be safely stored for 12 and eight weeks, respectively. At 14 per cent moisture content and 10 and 20 degrees Celsius, canola could be safely stored for eight and six weeks, respectively. However, canola at 30 degrees Celsius and 12 and 14 per cent moisture content could only be stored for two weeks and could not be stored safely at 40 degrees Celsius21.
Australian researchers have published moisture isotherms for canola and related this to varying oil contents22.
A guideline for oil content and safe storage moisture is: for every one per cent increase in oil content, the safe moisture content decreases by 0.1 per cent. For example, if canola with 40 per cent oil is safe at 8.5 per cent moisture, then canola with 45 per cent oil should be stored at eight per cent moisture. Although producers cannot easily measure oil content at harvest, it can be hypothesized that if cooler and wetter growing conditions occurred during the seed-filling stage, and the harvested canola seed is larger than normal, then the seed may have increased oil content.
Insects and mites
Insects can live in and feed on stored harvested canola seed4 but vary in ability to survive and establish infestations depending on the species and environmental conditions inside and outside of the bin. Generally, whole seeds are less vulnerable to infestation than crushed seeds, and only a few insect species are adapted to feed on the high oil content found in canola23. The optimal temperature for rapid growth of insects is from 30 to 35 degrees Celsius, and their activity is slowed by temperatures below 18 degrees Celsius. Therefore, if stored seed is cool and dry, insect populations should not grow and feed on the stored grain. Insect and mite infestations of stored seed will reduce the amount of time it is safe for canola to be stored7.
The main insects of concern for stored grain are the rusty grain beetle and red flour beetle, while the saw-toothed grain beetle can occasionally be found in stored canola if cereal grain or weed seeds have been stored with canola.
For whole seed, the merchant grain beetle (Oryzaephilus mercator) has been reported to multiply 1.87 times in 12 weeks, while the rusty grain beetle (Cryptolestes ferrugineus) failed to complete its life cycle.
Mites carry mould spores in and on their bodies, and may eat the surface and interior of canola seeds, potentially affecting seed weight and quality,24 and often feed on moulds. Heavy contamination by some mite species will leave a distinctly minty odour9. Canola was found to be more vulnerable to pest infestation than barley (Hordeum vulgare L.) when stored in farm bins in Manitoba, Canada during 1973-7625. Unlike barley, canola was heavily infested by grain mites and their predators. It was suggested that the prey mites multiplied by feeding (probably selectively) on fungal species and dockage (grain dust, broken grain kernels, weed seeds, etc.). The prey mite populations were effectively checked by predatory mites favoured by low temperatures, during the cooler months. Turning canola dispersed mould spores and mites throughout the bulk of the stored grain.
The distribution of the three most important British genera of stored-product mites in canola, wheat, and barley was studied at a range of relative humidities over a 10-year period26. In winter, grain feeding Acarus and Glycyphagus spp. were frequently present on seed surfaces dampened by moisture in both aerated and non-aerated bulks. In summer, the mites were usually most abundant below the surface, regardless of the relative humidity of the bulks. The difference between summer and winter distributions appeared to be related to the drying of the surface layers during the spring and summer. This may have caused the mites in those layers to reproduce at a lower rate. Populations of the predatory mite (Cheyletus eruditus) were usually more consistently distributed than those of Acarus and Glycyphagus, and appeared less sensitive to seasonal moisture and temperature changes. Aeration of nine per cent moisture seeds, at air temperatures below five degrees Celsius for four months, reduced the population of Acarus spp. to 4000 per kilogram, compared to 36,000 per kilogram in non-aerated bins.
Moulds, insects and mites in grain bulks seldom act alone, and interact with the grain and with each other27,((Sinha, R.N., & Wallace, H.A.H. 1977. Storage stability of farmstored rapeseed and barley. Can. J. Plant Sci., 57, 351-365.)).
Controlling insects
Insecticidal control
Currently, there are no registered insecticide options for storage insect control inside full canola bins. Therefore, it is important to ensure bins destined for canola are clean and clear of storage insects prior to loading. Diatomaceous earth is a treatment option for insect control if the bins is empty.
Keep Your Canola Export Ready by not using malathion on canola before or during storage or in the empty bins where canola will be stored. If the bin was treated previously, do not store canola in that bin within six months of treatment (within the same growing season). Malathion is lipophilic which increases the risk of absorption by oilseeds as compared to other grains like cereals, hence the need for these precautions.
Heat
Insects exposed to a grain temperature of 50 degrees Celsius for about 15 minutes will be killed. If canola requires heated-air drying, this may be an effective option.
Cold
Prolonged exposure to cold temperatures will kill most insects. However, grain bins over six metres (20 feet) in diameter will not cool sufficiently on their own to control some species. To ensure the entire volume is exposed to sufficient cold temperatures, aerate or turn the grain while the outside temperature is low.
The time required to kill insects depends on the grain temperature. For example:
- A grain temperature of minus five degrees Celsius takes about 12 weeks to kill most insects.
- A grain temperature of -10 degrees Celsius takes about eight weeks to kill most insects.
- A grain temperature of -15 degrees Celsius takes about four weeks to kill most insects.
- A grain temperature of -20 degrees Celsius takes about one week to kill most insects.
Physical Control
The physical impact of travelling through a pneumatic conveyor will control most mites and insects in your canola.
Grain conditioning systems
Conditioning systems can be classified by both the purpose and the state of the air used in the operation. Near Ambient Drying or Natural Air Drying (NAD) uses the surrounding (ambient) air to lower the temperature and moisture of stored grain with modest airflow rates. Aeration with lower airflow rates effectively alters temperature, while high temperature grain dryers use very high airflow rates and high temperatures to quickly lower seed moisture content. Supplemental heat use NAD fans with modest temperature increases to improve NAD alone.
Aeration systems
Aeration systems are used to preserve seeds by cooling and preventing moisture migration within a bin. They are used during seed storage, between harvesting and drying operations, and after heated-air drying. Aeration should begin as soon as there is enough canola to cover the floor of the bin, so that immediate cooling can take place. Fans should be operated continuously until the temperature of the canola is near the average outside temperature.
The purpose of an aeration system is to produce the lowest practical temperature and minimize temperature variation within the storage system. The amount of air required to change seed temperature will produce very little change in the moisture content of seed. Seeds with greater than 11 per cent moisture content should not use aeration alone unless seed temperatures are near or below zero degrees Celsius. Management of aeration systems differs in fall, winter, spring, and summer seasons10.
The airflow rates for canola aeration are normally 0.1- 0.2 cubic feet per minute per bushel (cfm/buA unit of measurement which describes the airflow rate (cubic foot per minute per bushel) in grain storage facilities (ex. bins). More) or one to two litres per second per cubic metre (Ls-1/m3). With an airflow rate of 0.1 cfm/buA unit of measurement which describes the airflow rate (cubic foot per minute per bushel) in grain storage facilities (ex. bins). More, about 150-200 hours of fan operation are needed to change the temperature throughout the bin10.
Operating aeration equipment during extended periods of high relative humidity (over 80 per cent) may promote mould growth, even in dry canola. However, one or two days of continuous aeration in high relative humidity will not damage the canola if dry weather follows for an equal duration. Since aeration is essentially a cooling procedure, the temperature of the air is more important than the relative humidity.
When the outside temperature has dropped five to 10 degrees Celsius below the temperature of the stored canola, the canola should be cooled again.
Aeration can be accomplished by moving air upward or downward through the grain bulk. There are advantages and disadvantages to each direction of air movement, but in most situations upward is preferred. Upward air movement permits the aeration progress to be easily determined by checking the canola temperature at the top of the bin. In addition, the fan can be started prior to filling, and air leaving the duct will help to keep the perforations clear of fines as filling progresses. The disadvantage of moving air upward is the potential for condensation to form on the underside of the roof when aerating warm seed in cold weather.
Moving air downwards and exhausting it at the bottom minimizes condensation. However, with downward air movement, canola at the bottom will be the last to cool and the hardest to check (to determine when aeration is complete). Another disadvantage is that when warm seed is added to the bin, the heat from the added seed is drawn through the previously cooled seed and warms it up again. When aerating grain in the summer, downward movement will draw the hot air from under the roof down through the rest of the seed28, which is also unfavourable.
Natural air drying or Near ambient drying (NAD)
Moisture can be removed from stored canola by passing ambient air at modest air flow rates through the bulk. Grain in a ventilated bin begins to dry where the air enters the bulk, usually at the bottom of the bin. A drying front develops and slowly moves upward through the bulk. Below the drying front, the grain will be at the temperature of the incoming air and at a moisture level in equilibrium with the incoming air.
Natural air drying or near ambient drying (NAD) alone can remove at least one to two per cent of moisture, but only if outside air has the “capacity to dry.” The air’s capacity to dry depends largely on temperature and relative humidity (RH). Temperature impacts the amount of moisture the air can hold as well as the rate of moisture removal. For example, warmer air has a higher rate of moisture removal. The Equilibrium Moisture Content (EMC), which is specific to each commodity, describes the moisture concentration at which grain will equilibrate to over time when air with certain RH and temperature is blown over it. If air has 50 per cent RH and a temperature of five degrees Celsius, and air is passed over canola for a length of time, the canola will eventually equilibrate to 8.1 per cent moisture (regardless of whether it started at 10 per cent or six per cent). Air with an RH greater than 70 per cent has limited drying capacity, and air less than 10 degrees Celsius will not effectively dry29.
The grain above the drying front will remain at a moisture level within about one per cent of its initial storage condition. The rate of movement of the drying front is mainly affected by the airflow rate per unit mass of seed. To dry the entire stored crop in the least possible amount of time requires a uniform air pattern throughout the bulk. The airflow pattern in a bin equipped with a completely perforated floor and a uniform grain surface will take the path of least resistance determined by the amount of fines in the central core and larger dockage on the outer walls. A peak in the central core of the bin can also increase resistance to airflow30. Rates of 0.5 – 0.75 cfm/buA unit of measurement which describes the airflow rate (cubic foot per minute per bushel) in grain storage facilities (ex. bins). More are recommended for efficient conditioning with NAD.
NAD fans should be started as soon as the harvested seed covers the floor of the bin (consult manual for aeration set ups in hopper bottom bins) and operated continuously until the temperature is less than 15 degrees Celsius and moisture content around eight per cent. Continue to cool until well below zero to store throughout the winter months.
Even under humid or rainy conditions the fan can be operated continuously to ensure that the main drying front will continue moving through the bulk despite the risk of rewettingThe process of bulk (seed) taking on moisture (increasing in moisture content) through the conditioning process. More the bottom slightly. As long as the fan is operated for a few days after the humid period, the moisture will redistribute through the bulk and will not cause spoilage. RewettingThe process of bulk (seed) taking on moisture (increasing in moisture content) through the conditioning process. More can be an economic benefit if the canola at the bottom has dried below the maximum allowed selling moisture level. Although it improves the storage quality, any drying below this regulatory value reduces the saleable mass, and thus the monetary value of the bulk30.
No conditioning operation is complete until the temperature and moisture level of the entire bulk have reached the desired level.
NAD with supplemental heat
The addition of supplemental heat to NAD systems can extend the amount of good drying days in the fall or allow for earlier spring conditioning by increasing the incoming air temperature and reducing its relative humidity (RH).
Ideally, airflow rates of at least 1.0 cfm/buA unit of measurement which describes the airflow rate (cubic foot per minute per bushel) in grain storage facilities (ex. bins). More are necessary to effectively move the drying front through the bulk and avoid seed damage near the fan inlet. With the airflow capacities of most NAD fans on canola bins, it is recommended that the inlet temperature be no more than 30 degrees Celsius, therefore NAD with supplemental heat is most suitable when ambient conditions are not much below zero31.
A good rule of thumb is that for every 10 degrees Celsius increase in ambient temperature, the RH is cut in half, allowing drying during a high humidity day or during rain events if the heater can be safely operated.
To determine the size of the heater required, the following equation can be used:
Heater capacity (btu/hr) = temperature increase (degrees Celsius) * airflow rate (cfm) * 2.05
This equation does not account for heat transfer loss, which can be as high as 50 per cent depending on the system and set up.
To avoid overdrying(In reference to grain storage) conditioning of the bulk (seed) to a moisture content lower than intended goal. More of the bottom layers of grain and ineffective drying of upper layers, grain should be turned every two to three days. Grain should be cooled after the use of supplemental heat, which can also remove an additional point of moisture.
It is not known how much more ventilation may be required when removing a lot of moisture with high temperatures. The general rule of thumb for ventilation is one square foot for every 1000 cfm of air flow, so it can likely be assumed that this would be the minimum requirement when adding supplemental heat31.
Grain dryers – heated air drying
Heated air drying is used when aeration or natural air drying fails to adequately condition canola. This may occur when ambient (outdoor) weather conditions are wet and cold or when canola is very damp following harvest. Hot air drying differs from natural air drying in that heated air will absorb considerably more moisture from the grain, and the warming of canola forces moisture out much more rapidly1. Bin, batch, and continuous heated air dryers may be used to dry canola. An efficient system of augers, hoppers and other handling equipment is necessary when heated air drying systems are used to ensure a continuous flow of grain from the field to the bin32.
The maximum air plenum temperature for drying canola depends on seed moisture content, seed viability temperature, expected storage period, type of dryer used, and other factors. Seed viability is adversely affected when the temperature of air used for conditioning is too high. Generally, a seed with high moisture content requires a longer drying process at a lower drying temperature, and drying temperatures need to be lower if no mixing of other seed occurs during the drying32. It is recommended to remove no more than five per cent moisture content per cycle to limit seed quality damage33.
Canola destined for seeding purposes should be dried at less than 45 to 50 degrees Celsius. For oil extraction, seeds can be dried at up to 82 degrees Celsius. Lower temperatures are used when canola is damp (over 12.5 per cent moisture) or when it is to be stored for over six months.
Overdrying(In reference to grain storage) conditioning of the bulk (seed) to a moisture content lower than intended goal. More should be avoided because it causes cracking of the seed coat. Damaged seeds undergo a marked rise in the level of free fatty acids causing a reduction in oil quality.
Table 3. Safe drying temperatures for canola
Grain dryers are designed mainly for wheat and corn (Zea mays L.) so they must be adjusted and calibrated to minimize canola losses. These losses may be through leakage or being blown from the drying chamber by the higher static pressure. Screens and floors of dryers more than 10 years old should be checked for rust perforation to prevent canola leakage34. Green weed seeds and canola stems and pods may interfere with the passage of canola through the dryer, and at high drying temperatures stationary canola may catch fire. Canola seeds may also ignite when they are passed by the burner.
Fire risk when drying canola may be reduced by cleaning the seed to remove light or fine material before drying, removing accumulations of debris from the walls and other areas of the dryer, using wind deflectors to prevent drawing airborne material through the burner, avoiding overdrying(In reference to grain storage) conditioning of the bulk (seed) to a moisture content lower than intended goal. More the seed and putting canola through the dryer on warm sunny days without starting the burner9.
Fan size
It is important to properly size fans for specific commodities, varying bin sizes and the desired outcome (ie. cooling or removing moisture). Fans being used for canola must operate at two to three times greater static pressure than in cereals. Consequently, systems designed for cereals may not produce adequate airflow rates through canola, and the risk of spoilage to the seed may be substantial.
Airflow rates will be limited with increasing resistance to airflow. Airflow resistance, measured in inches of water column, depends on the type/size of the grain (determining the size of the voids between the grain), the grain depth, and the ducting and aeration system/set up.
Each fan style and fan size has a range of static pressures at which it can operate35. For example, axial fans provide high airflow rates, but can only operate at relatively low static pressures. High speed centrifugal fans can operate at relatively high static pressures, but with lower airflow rates.
Static pressure can be directly measured or estimated. Knowing the static pressure, airflow rates can be determined, with the goal of 0.75 cfm/buA unit of measurement which describes the airflow rate (cubic foot per minute per bushel) in grain storage facilities (ex. bins). More for NAD, 0.1-0.2 cfm/buA unit of measurement which describes the airflow rate (cubic foot per minute per bushel) in grain storage facilities (ex. bins). More for aerating, and 1.0cfm/ bu for NAD with supplemental heat.
With a static pressure gauge installed nearest to the bin in the aeration ducting, manufacturer fan response curves can be used to estimate airflow rates based on the known static pressure. Alternatively, static pressure can be estimated using a desired airflow rate, grain type and grain depth. Static pressure can be estimated using a chart which shows the estimated effects of grain depth on static pressure.
Type of storage infrastructure
Canola is very sensitive to heating in storage36 and therefore requires specific bin construction (with different requirements than cereals have) to exclude moisture. The small seed size and free flowing characteristics of canola mean that high quality construction is necessary to prevent leakage. Roof and door openings, joints between structural components, and even bolt holes must be sealed to avoid losses. As heating and moisture migration problems tend to be more severe in larger storage structures, canola should be stored in the smallest bins available, without sacrificing convenience and efficient handling.
Bins
Storage in wooden granaries does not facilitate control of seed leakage, and is easily accessible for moisture, insects and rodents. Steel granaries, on the other hand, require almost no maintenance and can be easily sealed from pests, moisture and weather. Also, if conditioning of hot or damp grain is necessary, metal bins are best suited to the controlled movement of air through the grain mass. Regardless of the construction material used, storage structures must be as weatherproof as possible, yet still allow for safe and easy access to the bin for sampling and monitoring. A bin that is on a concrete base still requires weatherproofing. Concrete floors may resist the movement of water through it, but moisture can still enter the bin in the form of vapour. For this reason, it is important to place a vapour barrier, such as polyethylene, between the concrete and gravel base during construction.
Size
Research has shown that bin height does not affect the structural integrity of canola stored in tall bins. The compression forces experienced by canola seed in tall bins (up to approximately 100 feet tall) are not detrimental to canola. Some deformation of seed shape may be experienced, especially with increased moisture content, but seed coat rupture or oil exudation is uncommon. Higher seed moisture content seems to correlate with increased compaction, but decreased germination rate is not evident20.
Saskatchewan Agriculture and Food extension reported the impact of differing grain bin sizes on fan requirements. Two grain bins of equal volume but different diameters required different aeration fan sizes, because greater grain depth results in a higher static pressure.
The small size and round shape of canola seed also leaves fewer air pockets relative to wheat and other larger grains, which adds to the aeration capacity requirement. For example, a 2,000-bushel hopper bottom bin may require only a three-horsepower fan for wheat, but will need a five-horsepower fan to effectively condition canola.
Table 4. Effect of bin diameter on fan requirements
Research by the Prairie Agricultural Machinery Institute in 2017 determined that models of airflow dynamics and static pressure are applicable in bins up to 25,000 bushels in size.
This research investigated the impact on airflow and static pressure of gravity spread (to reduce the peak and evenly distribute chaff and fines throughout the bulk) and non-spread (e.g. traditionally augered) canola in 25,000 bushel bins. The gravity spreader provided a more level surface than the traditionally loaded surface and actual airflow rates were lower in the uniformly spread (non-peaked) grain. Static pressure values were less than what models would have predicted. There is no indication that the spread (non-peaked) canola provided any benefit to airflow and conditioning.
It was determined that the typical 10 horsepower centrifugal fans available for single phase power were not adequate to condition canola in a 25,000 bushel bin. After filling to about 17,000 bushels, or 70 per cent full, two 10 horsepower centrifugal fans operating in unison had reached their stall static pressureStatic pressure at which the air can no longer flow through the depth of grain in bulk storage. More and a single 10 horsepower centrifugal fan was nearing its stall static pressureStatic pressure at which the air can no longer flow through the depth of grain in bulk storage. More. Fan requirements may be limited by single phase power for large bins. Without upgrading fans and/or power, under filling bin space may be necessary to adequately condition the top layers of the bin37.
Grain storage bags
Grain storage bags have some advantages over traditional storage infrastructure. The initial investment is lower and they can be placed in the immediate area of harvest, limiting transportation requirements. Grain bags also allow for additional storage space for temporary leased land or added land without large capital investments and their size can be altered based on what is required. However, there are disadvantages too. Grain bags cannot be reused, so long term cost and waste can be substantial, they can be prone to damage from rodents, wildlife, and humans and monitoring and conditioning can be difficult. There is also a required investment in equipment to load and unload grain bags.
Storage grain bags are typically made up of three-layer polyethylene membranes, 235 micrometres (µm) thick. They typically hold between 200 to 300 tonnes of grain, measuring 2.7 to 3.0 metres in diameter, and between 60 and 76.2 metres long. Grain can be loaded into the bags at a rate of 200 tonnes per hour and unladed at 180 tonnes per hour using specialized equipment.
Preparation and careful selection of the storage site for bags is important, considering wildlife and rodent activity, drainage and seasonal access. Application of agricultural lime (calcium carbonate) has been reported to be effective against rodents38.
Grain bag storage of canola is a practical and safe option. Dry canola, approximately eight per cent moisture content, can be stored without quality deterioration for up to 40 weeks, Canola at 10 per cent moisture content for up to 24 weeks, at 12 per cent for up to 20 weeks, and damp canola (14 per cent) for no more than three to four weeks. Moisture migration occurs inside bags and will be larger with higher moisture content canola and higher temperature differentials. The temperature of the bulk is impacted by ambient conditions, being higher at the bottom in the colder months, and higher at the top during the warmer months38.
It is expected that initial loading temperature will have an impact on these safe storage guidelines, as the canola in this research was loaded at approximately 15 degrees Celsius.
Summer storage of canola
The best management practices for storing canola during summer include physically turning the bulk of grain, aerating it, or leaving it alone (for maintaining canola quality over the warm summer months on the Canadian Prairies), according to a study in the summer of 2014 and 2016. The best management practice for canola at less than 10 per cent moisture content was to maintain temperature at less than minus five degrees Celsius over the winter, and then to leave it alone thereafter. All treatments in this study resulted in no quality deterioration, but the bins that were warmed up showed the least stable conditions which could have led to heating and spoilage.
It is unknown how varying quality, temperature, moisture content and bin size impacts summer storage safety. The largest bins monitored in this study were 3700 bushels and additional bins of up to 10,000 bushels were also monitored.
Over the 78-day monitoring period in 2016, it was found that the side of the bins with predominant sunshine (the “sunny side”) was less than three degrees Celsius warmer than the other side (the “shady side”) of the bin, over the first 30 days. Over the entire monitoring period the difference between bin sides was negligible39.
Storage of canola in other geographies
Some interesting canola storage findings have been reported outside of Canada as well:
United States
- In Kansas, it is recommended that canola be stored at a moisture content of eight to nine per cent and temperatures of 10 degrees Celsius or less. For every six degrees Celsius or one per cent moisture reduction below 25 degrees Celsius and nine per cent moisture, the storage life was reported to double.
- Aeration fans are needed on any bin used to store canola, regardless of the storage time. Fully-perforated floors and aeration fans of 0.37 to 2.24 kilowatts are required to reduce temperature. It will take more than twice as long to move a cooling front through canola as grain, sorghum or wheat.
- Under Kansas conditions mites and mould develop on canola if moisture content is above eight and nine per cent, respectively. At 20 degrees Celsius, mites develop from egg to adult in about 14 days, however, if temperature is 4.5 degrees Celsius, development will take several months.
- High-temperature batch and continuous-flow dryers are frequently used. If the moisture content is above 17 per cent, it is advantageous to dry the seeds in two passes. The first pass reduces moisture content to 12 per cent, and then the canola can be transferred to a bin for drying with natural air. Too much moisture extracted at one pass can lead to shriveling and cracking of the seed as well as limit the drying performance. Natural air and low temperature drying work well with canola if the moisture content is below 15 per cent and the drying depth is less than three metres.
- In North Dakota, heating and spoilage occurs at moisture levels of nine to 10 per cent, and canola as low as 8.5 per cent moisture should be examined for heating at regular intervals. If harvested at high moisture, natural air drying or heated air drying is recommended. To maintain seed quality, a maximum drying temperature of 43 degrees Celsius is recommended for commercial production.
- In Montana, canola is harvested at optimum storage moisture of eight to nine per cent and stored in the smallest available bins with aeration. Fans are operated continuously until the temperature is near the average of the ambient air and long enough to be certain the cooling front moves completely through the bulk. Harvest temperatures may reach 27 to 32 degrees Celsius, therefore aeration should continue long enough to get the seed temperature below 21 degrees Celsius.
- In Maryland, seed will not store safely with more than 10 per cent moisture and will not be considered acceptable by canola buyers. If seed is harvested with more than 10 per cent moisture, it is likely to be discounted because of green seed. When marketed, seed quality is further discounted if seed moisture exceeds nine per cent moisture. It is essential that suitable drying facilities be available if seed moisture content at harvest exceeds 10 per cent.
- In South Carolina, seed quality and handling regulations include a one per cent discount for every 0.5 moisture percentage above nine per cent, with further financial discounts for the presence of heat damaged seeds over 0.1 per cent, and musty, sour or weevil infested seeds.
- In Georgia, it is recommended that only clean seed be stored and aeration and air movement are used for short-term storage. Seed moisture should not exceed eight to nine per cent for storage of more than a few days. Fans should be used in wet weather to prevent hot spotsAreas within bulk (seed) that have a higher temperature than the surrounding material (ex. in stored canola). More and mould development if seed contains more than nine per cent moisture. Periodically operate fans to remove any moisture that may have accumulated after drying to reduce the chance of mould growth. To control mite levels, bins should be thoroughly cleaned before seed is stored.
Europe
- In Western Europe, the climate is either temperate oceanic (United Kingdom, France, Denmark, western Germany) or temperate continental (Sweden, Poland, eastern Germany). Due to frequent wet weather, canola is normally harvested at a higher moisture level than in western Canada. To permit successful storage for a year or more requires drying from 20 per cent moisture down to seven per cent moisture. A moisture level of eight per cent permits storage for only a few months before spoilage occurs. Aeration is adequate for seed lots with moisture contents of up to 10 per cent, but seeds with greater than 12 per cent moisture should be pre-cleaned and dried with hot air in a continuous-flow dryer. Mite infestations are a serious problem at higher seed moisture levels. According to Swedish guidelines, the seeds should be dried to a moisture content where they remain viable. Seed viability rapidly decreases to 40 per cent from 100 per cent when moisture levels increase from nine to 12 per cent.
- A study at Yorkshire, U.K. found the moisture level of the incoming canola seed varied considerably from about eight to 30 per cent in extreme cases. A large proportion of the crop left the farm immediately for drying on contract by farmers or merchants using continuous-flow dryers. Safe drying temperature was up to 66 degrees Celsius to maintain the oil quality. But if the moisture level was above 17 per cent, temperature was reduced to slightly above 50 degrees Celsius to safeguard against germination. Very wet samples were often passed through the drier twice to reduce the likelihood of damage. Floor drying of rapeseed is frequently practiced in the U.K., with air blown through a 1.3 metre deep layer of seeds via mesh-covered ducts at the bottom of the bulk.
- Thomas, P.M. 1984. Swathing – combining, storage and conditioning of canola. Canola Growers Manual. 1101-1215. [↩] [↩] [↩] [↩] [↩] [↩]
- Prasad, D.C., Muir, W.E., & Wallace, H.A.H. 1978. Characteristics of freshly harvested wheat and rapeseed. Trans. ASAE, 782-784. [↩] [↩]
- Pronyk, C., Muir, W.E., White, N.D.G. & Abramson, D. 2004. Carbon dioxide production and deterioration of stored canola. Can. Biosystems Eng. 46: 3.25-3.33 [↩]
- Sinha, R.N., & Wallace, H.A.H. 1977. Storage stability of farmstored rapeseed and barley. Can. J. Plant Sci., 57, 351-365. [↩] [↩] [↩]
- Canadian Grain Commission. 1994.Official grain grading guide. Canadian Grain Commission, Winnipeg, Manitoba. [↩]
- Moysey, E.B., & Norum, E.R. 1975. Storage, drying and handling of oilseeds and pulse crops. In J.T. Harapiak (ed.) Oilseed and pulse crops in western Canada – a symposium. Western Cooperative Fertilizers Ltd., Calgary, Alberta. 507-540 [↩]
- Mills, J.T., & Sinha, R.N. 1980. Safe storage periods for farm stored rapeseed based on mycological and biochemical assessment. Phytopathology, 70, 541-547. [↩] [↩]
- Sathya, G., Jayas, D.S. & White, N.D.G. 2009. Safe storage guidelines for canola as the seeds slowly dry. Can. Biosystems Eng., 51, 3.29-3.38. [↩]
- Mills, J.T. 1989. Spoilage and heating of stored agricultural products. Prevention, detection, and control. Agriculture Canada, Ottawa, Ont. Publ. 1823E. [↩] [↩] [↩] [↩] [↩] [↩]
- Friesen, O.H., & Huminicki, D.N. 1986.Grain aeration and unheated-air drying. Manitoba Agriculture, Winnipeg, Man. Agdex 732-1. [↩] [↩] [↩]
- Canadian Grain Commission. 2019. ‘Prevent spoilage’ page featuring information from a Cereal Research Centre factsheet. Available online (November 2022 [↩]
- Mills, J.T., Clear, K.M. & Daun, J.K. 1984.Storability of frost damaged canola. Can. J. Plant Sci., 64, 529-536. [↩]
- Christensen, C.M., & Kaufmann, H.H. 1969.Grain storage. The role of fungi in quality loss. University of Minnesota, Minneapolis, Minnesota. [↩]
- Nash, M.J. 1978.Crop conservation and storage in cool temperate climates. Pergamon, Oxford. Pathak, P.K., Y.C. Agrawal, and B.P.N. [↩]
- Burrell, N.J., Knight, G.P., Armitage, D.M. & Hill, S.T. 1980. Determination of the time available for drying rapeseed before the appearance of surface moulds. J. Stored Prod. Res., 16, 115-118. [↩]
- Manitoba Agriculture. 1980. Harvesting, storage and grades. In Rapeseed ’80. Manitoba Agriculture, Winnipeg. 601-638 [↩]
- O’Donovan, J.T., Harker, K.N., Clayton, G.W. and Blackshaw, R.E. 2006. Comparison of a glyphosate-resistant canola (Brassica napusAlso referred to as Argentine canola, it is the species of canola currently commonly grown in Canada. More L.) system with traditional herbicide regime. Weed Tech., 20, 494-501 [↩]
- Thomas, P.M. 1984. Swathing – combining, storage and conditioning of canola. Canola Growers Manual. 1101-1215 [↩] [↩]
- Jayas, D.S., Sokhansanj, S. Moysey, E.B. & Barber, E.M. 1987. Distribution of foreign material in canola bins filled using a spreader or spout. Can. Agric. Eng., 29, 183-188. [↩]
- Gregg, N., Hill, L., & Leduc, P. 2012. Long term storage of canola. Final Report. PAMI. Humboldt, Saskatchewan [↩] [↩]
- Sun, K., Jian, F., Jayas, D.S., White, N.D.G. & Fields, P.G. 2014. Physical properties of three varieties of high-oil canola and one varietyA variety is a variant of a species that evolved in nature without the intervention of humans, e.g. Brassica oleracea variety (in short form, var.) botrytis (cauliflower), var. capitata (cabbage), var. italica (broccoli), etc. More of low-oil canola. Transactions of the ASABE. 57, 599-608. 10.13031/trans.57.10547. [↩]
- Cassells, J.A., Caddick, L.P., Green, J.R. & Reuss, R. 2003. Isotherms for Australian canola varieties. In Stored grain in Australia 2003, Proceeedings of the Australian Postharvest Technical Conference. E.J. Wright, M.C. Webb and E. Highley, eds. June 25-27, 2003, Canberra, Australia. 59-63. [↩]
- Sinha, R.N. 1972. Infestibility of oilseeds, clover, and millet by stored product insects. Can. J. Plant Sci., 52, 431-440. [↩]
- Hudson, R.D., Woodruff, J.M., Shumaker, G.A., Hodges, S.C., Murphy, T.R., Monks, D., Bertrand, P., & Hammond, C. 1991.Canola a new crop for Georgia. Canola Production Guide. Georgia Extension Canola Committee. [↩]
- Sinha, R.N., & Wallace, H.A.H. 1977. Storage stability of farm-stored rapeseed and barley. Can. J. Plant Sci., 57, 351-365. [↩]
- Armitage, D.M. 1984.The vertical distribution of mites in stored produce. In D.A. Griffiths and C.E. Bowman (eds) Acarology VI, 2, 1006-1013. [↩]
- Fleurat-Lessard, P. 1973.Les Acariens des stocks de graines de colzas. Centre Technique interprofessionnel des Oleagineux Metropolitans, Paris. 31, 44. [↩]
- Friesen, O.H., & Huminicki, D.N. 1986. Grain aeration and unheated-air drying. Manitoba Agriculture, Winnipeg, Man. Agdex 732-1. [↩]
- Prairie Agricultural Machinery Institute. 2017. Equilibrium Moisture Content Charts for Grain Storage Management. [↩]
- Mills, J.T. 1990.Protection of farm-stored grains and oilseeds from insects, mites, and moulds. Agriculture Canada, Ottawa, Ont. Publ. 1851E. [↩] [↩]
- Prairie Agricultural Machinery Institute. 2018. Supplemental Heat FAQ. [↩] [↩]
- Friesen, O.H. 1981.Heated-air grain dryers. Agriculture Canada, Ottawa, Ont. Publ. 1700. [↩] [↩]
- Hellevang, K. 2019. North Dakota State University. Personal Communication [↩]
- Harner, J.P. III. 1989.Handling and storage. p. 11-13. Kansas State University Cooperative Extension Service, Manhattan, Kansas. Bull. 706. [↩]
- Prairie Agricultural Machinery Institute. 2018. Airflow Resistance Charts for Grain Storage Management [↩]
- Mills, J.T. 1976.Spoilage of rapeseed in elevator and farm storage in western Canada. Can. Plant Dis. Surv., 56, 95-103. [↩]
- Greiger. 2017. On-Farm Canola Storage Research in Large Bins. Unpublished [↩]
- Jian, F., Chelladurai, V., Jayas, D. S., & White, N. D. G. 2015. Three-dimensional transient heat, mass and momentum transfer model to predict conditions of canola stored inside silo bags under Canadian Prairie conditions, Part II – model of canola bulk temperature and moisture content. Transactions of the ASABE 2015, 58(4), 1135-1144. doi:10.13031/trans.58.11053 [↩] [↩]
- Agnew, J. 2016. Summer Storage of Canola. Unpublished [↩]