Key Result
Supplemental heat added to natural air drying systems can improve drying capacity for canola as long as airflow is a minimum of one cubic foot per minute per bushel (cfm/bu.). Air must be heated to at least 5°C but not more than 30°C for in-bin drying.
Project Summary
Overview
This two-year canola and wheat storage project found that adding supplemental heat to natural air drying (NAD) systems can be a lower-capital alternative to dedicated heated-air dryers, but careful management is required to keep operating costs comparable to that of a dedicated dryer system.
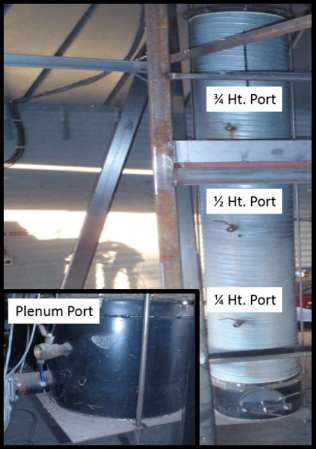
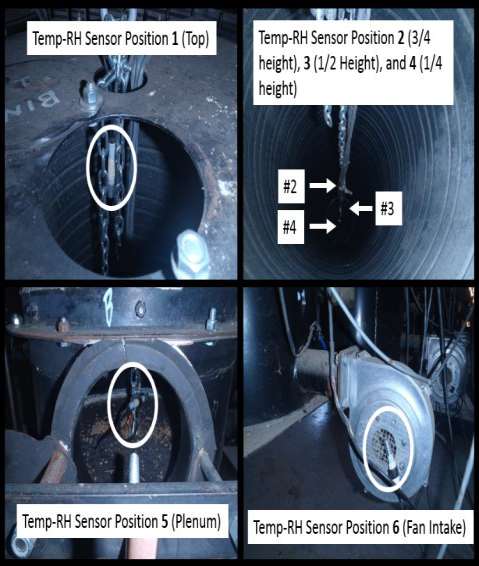
First year trials, using bench-scale test bins, compared the effect of air flow rate on supplemental heating with NAD compared to NAD without added heat.
Second year trials assessed the rate of drying with supplemental heat at three different temperature increases.
All trials were planned to occur in mid-late fall to ensure the ambient conditions were representative of conditions where supplemental heating is typically used. Moisture content, grain weights, and grain temperature data from each bin were recorded for the six treatments (three airflow rates and two temperatures). Ambient temperature and humidity data were averaged for the three standard bins at the fan intake as well as for the three bins with supplemental heat.
First year results indicated that adding 10°C of heat when ambient conditions are cool and damp will increase the drying rate, as long as the airflow rate is at a minimum of one cubic foot per minute per bushel (cfm/bu.) and sufficient to move the moisture all the way through the grain bulk. Airflow rate has an impact on drying rate, particularly for wetter grain. Airflow rate will depend on the type of fan used, the density of the grain and grain depth within the bin. (If airflow is too low, consider removing some grain from the bin.)
The trials also showed that over-drying at the bottom of the bin may not be avoidable, therefore an average dry moisture should be targeted, followed by mixing the grain.
Second year trials showed that a 10°C increase in temperature is adequate as long as the result is a plenum temperature of greater than 5°C. However, if sub-zero ambient conditions are being experienced for prolonged periods of time, then higher temperature increases would be required. Based on the observed rates of drying for both canola and wheat in the trials, supplemental heating with a NAD system may not be suitable for starting grain moisture contents more than three percentage points above “dry” because an increased risk of spoilage is possible. Careful monitoring or reduced grain bed depths can help mitigate this risk if a heated-air dryer is not available.
Fuel comparison. The study included an economic assessment of supplemental heating with various fuel types. It found that fuel type has the greatest impact on operating costs. Natural gas has lower cost than diesel and propane, however, access to natural gas can be capitally hindering in certain regions. Estimated efficiencies for NAD systems with supplemental heat range from 50 to 75 per cent compared to efficiencies of 40 to 55 per cent for dedicated heated-air drying systems.
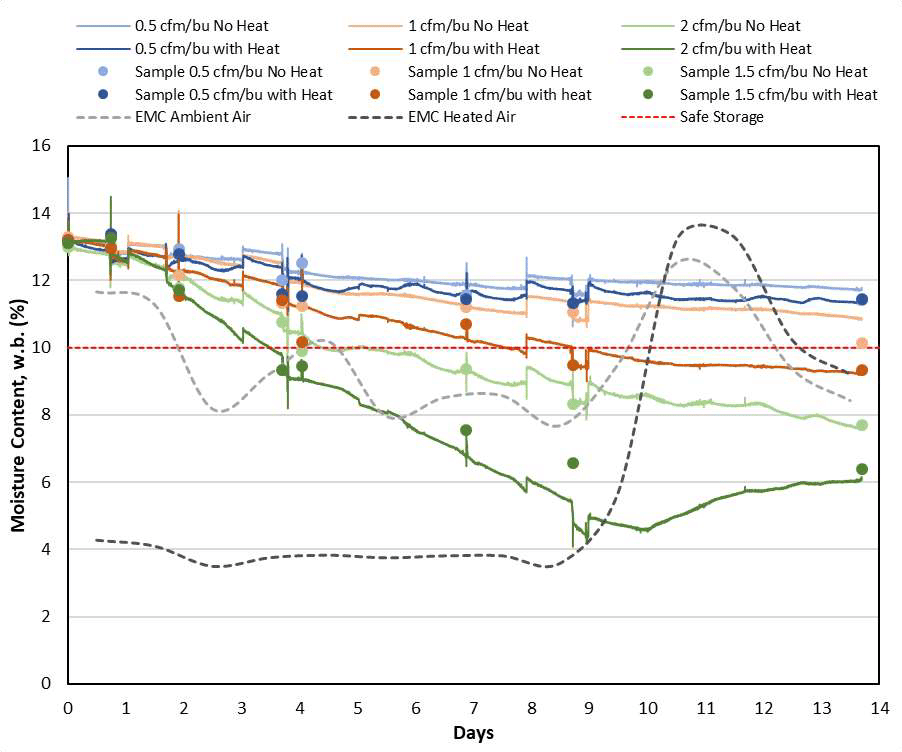
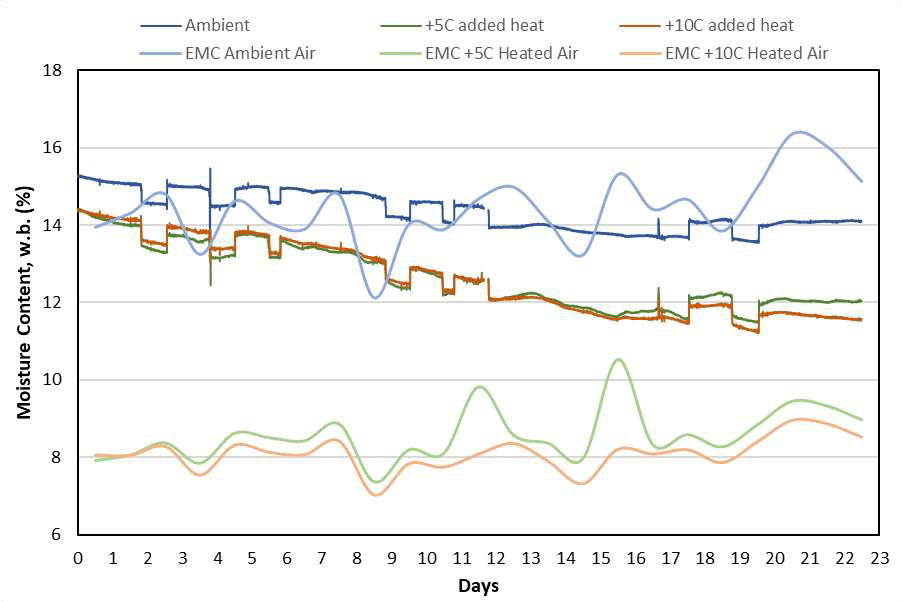
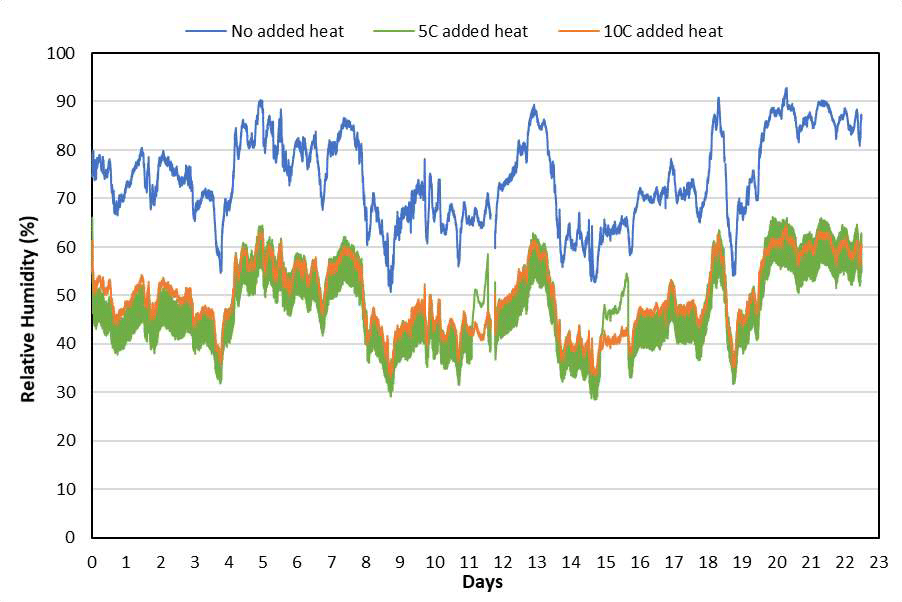
Recommendations
Based on results of this project and other expert judgement where specific information is still lacking, these are the recommended general management practices when using NAD systems with supplemental heat:
- For safety and grain quality reasons, only use a CSA-certified heater designed for use with grain storage fans. Follow manufacturer’s instructions for installation and operation.
- Unless an adequate airflow rate can be ensured (minimum 1 cfm/bu), there is a risk of overheating the grain.
• Low airflow rates may not have enough energy to fully remove moisture from the bin. - A plenum temperature of 10°C to 20°C should be targeted; however, limit the air temperature increase to 15°C or less.
• Higher temperature increases result in high fuel costs, reduced heat transfer efficiency, increased chance of over drying, and increased chance of condensing and freezing at edge of bin. - Do not exceed an inlet (after heater) temperature of 30°C.
• Even though higher temp equals greater drying capacity, you do not want to overheat the grain.
• Air flow rates of 0.75 to 1 cfm/bu can “keep up” with moderate drying rates, but not with high drying rates associated with high temperatures (>30°C). - As much as possible, maintain a consistent air temperature flowing to the bin.
• Thermostatic controllers are becoming more common and will help achieve a consistent temperature being delivered to the bin. This will help minimize day-tonight temperature variations. - Since condensation on a cold bin roof can cause moisture problems in the stored grain, ensure adequate ventilation in the headspace.
• A minimum of 1 ft2 of vent space for every 1,000 cfm of airflow is required.
• Consider the use of “active” ventilation in the headspace to expel moist air more effectively. - Consider turning the bottom grain once the average bin moisture is dry to distribute over-dry grain.
- Ensure that the drying front is pushed through the bin before stopping aeration. As noted in the testing, stopping the NAD with an incomplete cycle can leave grain with localized moisture levels higher than what was originally present in the grain.
- Grain must be cooled to less than 15°C after drying.
• Cooling will also remove some moisture, so drying may be complete when moisture is within one per cent of target. - Monitor grain conditions with in-bin cables and/or samples during drying.